The surface treatment of telescopic aluminium tube manufacturers includes oxidation, secondary oxidation, surface drawing, sandblasting, high gloss, spraying, printing, electroplating and electrophoresis.
1. Surface treatment and oxidation of telescopic aluminium tube
The aluminum itself has a layer of aluminum oxide film, which has certain corrosion resistance. However, this layer of aluminum oxide film will make the surface of the aluminum profile lose its original luster, and all aluminum alloy products usually need special oxidation treatment for oxidation coloring. Let it have corrosion resistance, wear resistance and other functions. The oxidation process is: degreasing (degreasing), alkali etching, anodizing, activation, dyeing, and sealing
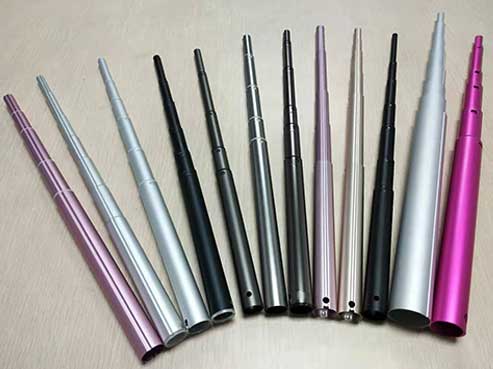
2, surface treatment of telescopic aluminium tube, surface drawing
According to the decorative needs of the aluminum telescopic rod surface, several drawing effects such as straight grain, random grain, thread, corrugation, and swirl can be produced.
3, telescopic aluminium tube surface treatment sandblasting
In order to meet the requirements of soft gloss, sandblasting can be used to obtain the surface effect of the light film or the reflective surface. Surface sandblasting can overcome most common defects on the surface of aluminum.
4, aluminum telescopic tube surface treatment high gloss
The highlight treatment is usually carried out on flat aluminum parts, and the effect of milling machine processing is performed on the edges of the aluminum parts and other places that need to be treated prominently.
5, aluminum telescopic tube surface treatment spraying and printing
There are two ways of spraying: baking varnish and powder spraying, and printing includes silk screen and pad printing.
6, telescopic aluminium tube surface treatment electroplating electrophoresis
The common processes for electroplating of aluminum telescopic rod manufacturers are: degreasing (degreasing), alkali corrosion, activation, zinc replacement, activation, electroplating (such as nickel zinc copper), chrome plating or passivation, drying, packaging